The Ultimate Guide to Choosing the Right Packaging Machine Repair Experts
The Ultimate Guide to Choosing the Right Packaging Machine Repair Experts
Blog Article
Quick and Reliable Product Packaging Maker Repair Service Provider to Minimize Downtime
In the affordable landscape of manufacturing, the performance of packaging operations rests on the reliability of equipment. Quick and dependable repair service solutions are vital in reducing downtime, which can bring about considerable operational obstacles and economic losses. Understanding the significance of prompt treatments and the function of specialist specialists can transform just how companies come close to maintenance and repairs. Nonetheless, browsing the myriad alternatives readily available for repair service solutions can be difficult. What elements should services take into consideration to ensure they are making the ideal option for their operational requirements?
Significance of Timely Repairs
Timely repairs of product packaging equipments are essential for maintaining functional performance and reducing downtime. In the fast-paced environment of manufacturing and packaging, also small malfunctions can lead to considerable hold-ups and efficiency losses. Addressing problems without delay ensures that equipments operate at their optimal capability, consequently securing the flow of operations.
Furthermore, prompt and regular upkeep can avoid the escalation of small problems right into significant malfunctions, which frequently sustain greater repair costs and longer downtimes. A proactive strategy to machine repair service not only maintains the integrity of the tools however additionally boosts the overall integrity of the manufacturing line.
Furthermore, prompt repair work add to the longevity of product packaging equipment. Equipments that are serviced quickly are less likely to deal with too much deterioration, allowing organizations to maximize their investments. This is especially vital in sectors where high-speed packaging is vital, as the requirement for constant efficiency is vital.
Benefits of Reliable Provider
Reputable solution providers play a critical function in ensuring the smooth procedure of packaging equipments. Their know-how not only boosts the efficiency of repair work however likewise contributes considerably to the durability of equipment.

In addition, a respectable company uses comprehensive assistance, including training and assistance for staff on maker procedure and upkeep ideal practices. This not only encourages employees yet additionally grows a culture of security and performance within the organization. Generally, the benefits of engaging trustworthy solution companies extend beyond prompt repairs, favorably influencing the whole operational workflow of packaging processes.
Usual Packaging Equipment Problems
In the world of packaging operations, different problems can compromise the efficiency and capability of makers. One widespread issue is mechanical failing, often originating from deterioration or inadequate upkeep. Parts such as equipments, electric motors, and belts may stop working, causing breakdowns that halt production. An additional common problem is imbalance, which can cause jams and irregular product packaging, impacting item high quality and throughput.
Electrical troubles can likewise interfere with packaging operations. Defective wiring or malfunctioning sensing units might result in unpredictable device behavior, creating delays and raised operational expenses. Additionally, software program glitches can prevent the maker's shows, causing functional inadequacies.
Inconsistent product circulation is an additional critical concern. This can develop from variations in item form, weight, or dimension, which might impact the machine's capacity to take care of things precisely. Lastly, not enough training of drivers can aggravate these problems, as inexperienced employees may not recognize very early indicators of breakdown or might abuse the tools.
Resolving these navigate to this site typical product packaging machine issues quickly is important to keeping efficiency and ensuring a smooth operation. Routine inspections and proactive maintenance can significantly reduce these issues, cultivating a trustworthy packaging environment.
Tips for Minimizing Downtime
To decrease downtime in product packaging operations, implementing a positive maintenance method is essential. Routinely set up upkeep checks can identify prospective issues before they rise, ensuring machines operate efficiently. Establishing a regimen that consists of lubrication, calibration, and assessment of crucial components can considerably decrease the frequency of unexpected failures.
Educating staff to run equipment appropriately and recognize very early indication of breakdown can likewise play an essential duty. Equipping drivers with the understanding to perform standard troubleshooting can avoid small concerns from causing major hold-ups. Maintaining an efficient Full Report inventory of vital spare components can accelerate fixings, as waiting for parts can lead to extended downtime.
Furthermore, documenting machine efficiency and upkeep activities can aid identify patterns and recurring issues, permitting targeted treatments. Incorporating innovative monitoring innovations can give real-time data, making it possible for predictive upkeep and minimizing the risk of sudden failings.
Last but not least, fostering open communication in between drivers and upkeep groups makes certain that any abnormalities are immediately reported and attended to. By taking these positive steps, services can enhance functional efficiency and significantly lower downtime in packaging processes.
Choosing the Right Repair Service Service
Selecting the ideal repair work service for product packaging machines is a critical choice that can dramatically impact operational performance. Begin by examining the read what he said service provider's experience with your specific type of packaging devices.
Next, consider the provider's credibility. Seeking comments from various other services within your industry can supply understandings into dependability and top quality. Qualifications and collaborations with identified tools producers can additionally indicate a dedication to quality.
In addition, analyze their action time and availability. A provider who can offer punctual assistance lessens downtime and maintains production flow constant. It's likewise essential to inquire about warranty and service guarantees, which can mirror the self-confidence the company has in their job.

Conclusion
Finally, the value of trusted and quick packaging maker repair service services can not be overemphasized, as they play a vital function in reducing downtime and ensuring functional performance. By focusing on timely fixings and choosing reliable provider, organizations can effectively deal with usual problems and maintain efficiency. Carrying out aggressive maintenance methods and buying staff training more enhances the durability of product packaging equipment. Eventually, a tactical approach to fix services cultivates a more durable production environment.
Prompt repair services of packaging makers are critical for preserving operational efficiency and lessening downtime.In addition, prompt repair services add to the durability of packaging equipment. Generally, the advantages of engaging trusted service providers expand past prompt fixings, favorably affecting the entire functional operations of packaging processes.
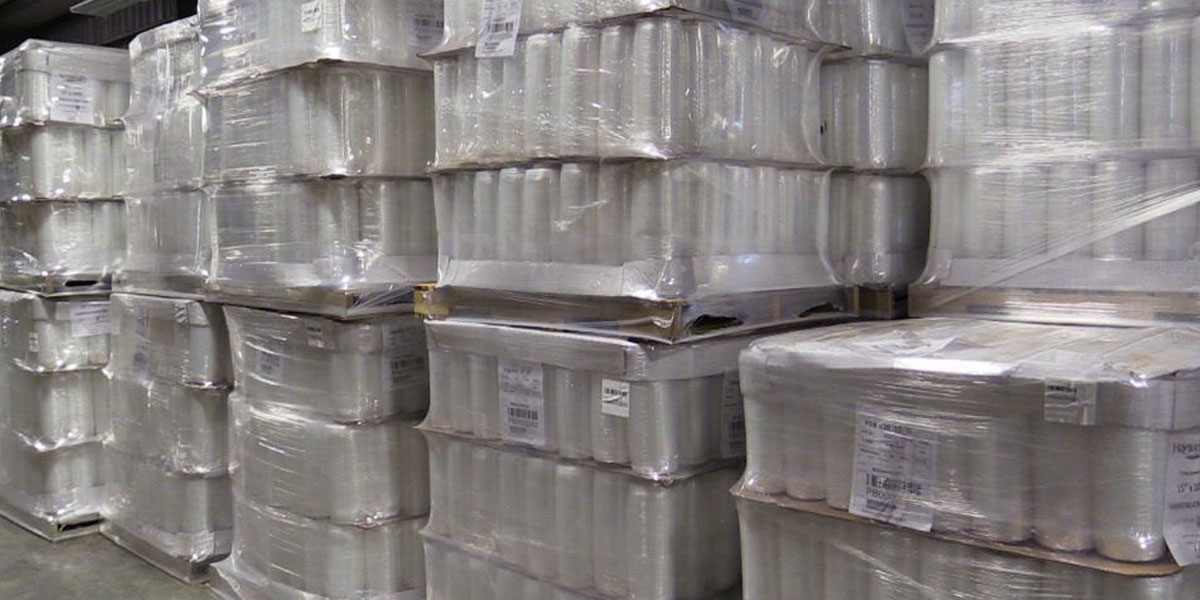
Report this page